Trying a different tactic:
This post is an update to previous post. Starting the brazing over was a step in the right direction. We used a different set up for the blow torch to get it even hotter. We used a setup that allowed the torch to get the fuel and oxygen at the same time resulting in an even hotter fire. Once we filed off our previous brazing job everything went along smoothly. That was until we heated it up so many times that whenever we would try to fix a part that was leaking, another problem would be made. We finally got it to a point where there was only one hole left in our brazing job. We would try to fix it and none of the brass would stick in the hole. Some kind of contamination in that one spot that made the brass not stick. We tried to fill the hole with lead solder and that didn't work at first. We used a hand drill to drill all the way through the hole to get the contaminated area out. We tried the solder again to avoid heating the brazing job to a temperature that would melt the brass because lead solder melts at a lower temperature than the brass. Finally we pressure tested the tank for the last time and we came out victorious. The gas tank no longer has a crack in it and it is completely leak proof!
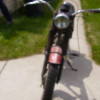
