Rocker Boxes
There is not much mechanically mysterious in the Triumph rocker boxes, but they do have a few wrinkles, and are subject to leaking in a couple of places. One potential leaking location is the gasket surface. One way to help ensure a tight seal here is to linish both the surface of the rocker box and the head. Don't remove any more material than necessary, since rocker geometry could be affected if too much is removed.
The second place where some Triumphs chronically leak is where the head of the rocker sindle is held in the rocker box housing. This area is sealed with an O ring, which is probably adequate, except that it can be a challenge to install the spindle without damaging the O ring. What often happens is that the part of the O ring that is proud of the spindle head, rather than compressing into the O ring groove, just gets sheared off by the housing bore. Some say that this is normal, or even part of the design, but I don't buy it. There is apparently a factory tool that works by precompressing the O ring before it goes into the housing. Some builders accomplish the same thing by putting a chamfer on the edge of the housing bore to ease the compression of the seal. Others try to "worry" the O ring into the bore with a small dull screw driver or some similar tool as the spindle is brought home. After attempting the worrying process without much success, I tried the chamfer with some sandpaper on a tapered mandrel, and it appeared to work. However, when I removed the spindle, the damage to the O ring was obvious. I decided to get more scientific about it.
I calculated the range of angles for the chamfer taper that would give an opening close to the size of the uncompressed O ring, while not going deep enough into the bore to change its diameter at the O ring seating position, then looked for a tapered hand reamer that wold work. Also, I needed some way to keep the reamer aligned in the bore so I didn't end up with a cockeyed taper.
This is what I ended up using. The reamer has an included angle of about ten degrees--just about the minimum that would work. The little mandrel was made to fit the spindle bore in the center and opposite end of the housing, keeping everything aligned. The top of the mandrel has a countersunk depression for the tip of the reamer to go into. The spring just keeps the mandrel pushed up against the reamer so it wouldn't wander off.
First I blued the bore so it would be easy to gage progress, then started movin' metal.
By measuring the spindle, I knew I could only go a maximum of about 0.200" into the bore before I got close to the O ring seating position. The reamer I had was not a precision instrument, so it left a fairly rough surface, so when I got close to the final taper to size, I polished the taper with fine carbide paper wrapped around the reamer.
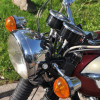
