Wiring II
I had previously refurbished the original wire harnesses on tjis bike by removing what was left of the woven loom and replacing it with an expandable braided sleeve material with heat shrink at the joints. This worked very well for the front harness coming from the headlight shell, but for the more complicated rear harness, there were problems. First of all, I rebuilt the harness off the bike, using the existing lay of the wires as a guide. This proved to not be a good approach. Some of the branches weren't in exactly the right place, and some of those that were came off the main harness at a wrong angle, making routing awkward. On top of this and most seriously, some of the wires had hard, brittle insulation that actually cracked when I tried to manipulate them into place. This was probably due to a combination of age, heat and organic vapors.
I decided to start over from scratch on the rear harness. It's not hard or even that expensive to get the original wire colors in a gauge similar to the original. British wire today is sized by the number of 0.3 mm strands that make it up. The original harness used 14-strand wire, which is close to AWG 18-gauge. For a few of the wires that carry heavier current, I went to larger 28-strand wire.
I ran the wires in place on the bike so that all the branches would be in the right place, going the right direction. I then bound the wire bundles with a bazillion tie wraps before removing it from the bike. Then I put on the braided sleeve with heat shrink at the junctions. A little electirical tape sealed the junctions. I used a non-adhesive tape that sticks to itself, but not the wires. This allows the wires to flex and move, which keeps the harness from getting stiff.
After sleeving the main harness, I started at the rear of the bike by soldering bullets on the wires and connecting them to the rear lights. I then ran the harness out through the grommet and down the inside of the left top frame rail.
Before I went any further, I took the time to check out some of the electrical components to make sure they were good. Here is the bridge rectifier under test. A meter with a diode test function is best for this. Start with one of the outside terminals and test to each of the center terminals Then reverse the test leads and repeat. For each pair of terminals, one direction should read "Overload" or something similar, while the other direction should read some small number, and the meter may beep. Repeat with the other outside terminal.
The first drop from the main harness was for the rear brake switch. I just left this long to trim later, since the chain guard is not installed yet. Next up going forward was the breakout for the rectifier and flasher units. I used new good quality open barrel tinned copper terminals with the proper crimping tool. I usually solder the crimped connections for a little extra insurance.
The alternator branch routes down the vertical frame tube to a couple of barrel connectors.
This is what's left to make sense of.
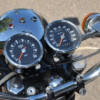
