Meet helmet "Jack , Culling the weak since 1790"
Overview: This was a 3D scan project, starting with a 3D scan of a base helmet (Shoei off-shelf performance
helmet) and then scanning a clay sculpt on top of the base helmet, and digitally subtracting the difference to
re-create the parts for subsequent assembly via 3D printing.
Key points for this helmet idea are:
1. The whole sculpt adds less than 1 lb of extra weight,
2. Itis designed around a full performance off-shelf safety helmet
3. All base helmet features such as visor and vents still function as designed
4. Aerodynamic design, and surely terrifying to witness on the road
The process involved using a structured light scanner (SLS) to capture the bare helmet exterior in high detail. After setting up a field of view large enough to scan the entire helmet on a rotary programmable platform, and custom
calibrating the scanner, many views were taken of the helmet from a variety of angles. Each view captures a dense point cloud, and all views are aligned roughly, then globally, before cleaning up data for a complete merge. The
photo of the bare helmet before scan, shows some clay dots placed randomly, which are not always needed but can be helpful references for ensuring correct alignment. Due to the black color, and shiny surfaces on the helmet,
white powder spray (not shown) is used to create a uniformly bright, matte surface for the scanner to easily capture it. The spray is so thin that dimensions are not compromised.
The merged scan file needs post-processing to refine the digital data by stripping out disconnected data islands, cleaning of any abnormal triangles, removing self-intersections, and repairing any tiny holes that remain. The
output file is in STL format, and the final file size can be controlled by decimating the triangles that make up an STL. Specialized software can perform "smart decimation", which increases triangle size in plain areas while
retaining small triangles in high detail areas, -helpful when trying not to exceed maximum file size for 3D printers and other reproduction methods. It takes software, but also training and experience to get to a nice clean STL file
that retains good detail from a scan.
Once the baseline helmet scan was completed, next step was to scan the sculpted clay master "Jack" on top of an identical helmet, align both scans to each other, and digitally isolate the difference. This isolated STL is then
inspected.
Headless Helmets initially experimented with making custom helmet sculpts in traditional silicone molds as seen below, however these involved a large amount of labor, and results were not always light enough to avoid adding more than 1lb to the helmet.
In summary, employing 3D scanning and 3D printing to the workflow added several benefits:
Digital capture and archive of custom hand sculpts for future use
Digital baselines of existing, bare helmets for creation of new sculpts
Ability to digitally divide the sculpts for subsequent 3D printed parts, and be sure that everything will fit
Consistent 3D printed parts produced
Much labor saved versus traditional mold making and casting
Faster production cycle from sculpted master design, to reproduced helmets
Leading to big smiles all around. Right Jack?
We wish great success to all the artists and engineers at Headless Helmets, and hope to see more terrifying designs from them soon!
Check out their website: www.HeadlessHelmets.com
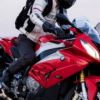
