Wiring 2
The fourth replacement wire had a bullet connector on the other end to interconnect with the rear harness. The replacement connector ia not identical to the original, but is compatible. This bullet terminal can be crimped or soldered. The picture is before soldering.
The last wire had to terminate on the socket for the oil pressure warning lamp. I had to desolder and uncrimp the old wire to replace with the new one. The other picture shows the harness with all of the ignition switch wires replaced. Since I didn't know how long the leads to the switch were, I left them long, and will trim and terminate them after a trial fit-up on the bike.
This is the rear harness with all of the electrical tape removed, but with the remnants of the original loom. One problem on this harness was the cracked insulation on the red wire shown in the middle picture. The insulation on this wire had become hard so that rather than flexing, the insulation broke open. The hardness of the insulation and its discoloration suggested that it had been "cooked" with high temperature. This wire was the ground return between the rectifier and the battery, and handled all alternator current for the entire system except for the rear lights. I consider 18 gage to be a little light for this service, and the fried insulation supports this. I replaced this conductor with a 16 gage wire. The modern 16 gage automotive wire actually had almost the same outdside diameter as the older wire, so it's hard to tell the difference.
The "tug test" of all terminals also turned up one other bad termination, so I replaced the terminal.
Though it would look nice to have a nice new woven cotton loom for the harnesses, it's not really practical to have it done to an old harness. Besides, the loom seems to be the shortest-lived component of the harnesses. I considered applying heat shrink tubing to the harnesses, but this seemed to have one of the same drawbacks as taping them--it would restrict wire movement within the harness. There are also higher-tech harness wrapping tapes available that adhere to themselves, but not to the wires in the harness. This was attractive, but in the end, I opted to use a synthetic woven loom material in combination with heat shrink tubing at the junctions. I used two kinds of loom material. One is split lengthewise, but has a permanent curl that wraps around the wire bundle. The other kind is not split, but expands like the chinese finger handcuffs to maybe four or five times its relaxed diameter. This method gives a neat-looking harness with good protection for the wires, while retaining good flexibility.
Refurbed main harnesses, ready for install:
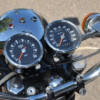
